Introduction

In the realm of gear manufacturing, selecting the right material is paramount to ensure durability, efficiency, and cost-effectiveness. Among the myriad of options available, 8620 steel stands out as a popular choice for numerous reasons. This blog delves into the properties and advantages of 8620 steel that make it an ideal material for gear manufacturing applications.
Understanding 8620 Steel: Composition and Properties
8620 steel is a low alloy nickel-chromium-molybdenum steel renowned for its exceptional strength, toughness, and wear resistance. Its composition typically consists of approximately 0.20% carbon, 0.55% to 0.75% silicon, 0.50% to 0.70% manganese, 0.35% to 0.65% phosphorus, 0.035% sulfur, 0.40% to 0.60% chromium, 0.15% to 0.25% molybdenum, and small amounts of other elements.
Element | Composition (%) |
---|---|
Carbon (C) | 0.20 |
Silicon (Si) | 0.55 – 0.75 |
Manganese (Mn) | 0.50 – 0.70 |
Phosphorus (P) | 0.35 – 0.65 |
Sulfur (S) | 0.035 |
Chromium (Cr) | 0.40 – 0.60 |
Molybdenum (Mo) | 0.15 – 0.25 |
Strength and Toughness: Key Attributes for Gears
8620 steel is a highly favored material in gear manufacturing for several compelling reasons, primarily due to its exceptional combination of strength and toughness. This alloy contains nickel and chromium, which play pivotal roles in enhancing its properties.
The presence of nickel and chromium contributes significantly to the hardenability of 8620 steel. Hardenability refers to the ability of a material to develop hardness through heat treatment processes such as quenching and tempering. This results in a material with high core strength, essential for withstanding the demanding conditions gears often encounter.
Moreover, the addition of molybdenum further enhances the toughness of 8620 steel. Toughness is the ability of a material to resist fracture under stress, particularly in the presence of defects or at low temperatures. In gears subjected to heavy loads and repeated stress cycles, toughness is paramount to prevent failure.
The combination of high core strength and improved toughness makes 8620 steel highly resistant to impact and fatigue failure. Impact resistance is crucial for gears operating in environments where sudden shocks or vibrations are common, while fatigue resistance ensures longevity even under continuous cyclic loading.
Wear Resistance: Prolonging Gear Lifespan
-
Alloy Steel 31CrMoV9/1.8519
-
Alloy Steel 17CrNiMo6/1.6587
-
Alloy Steel 25CrMo4/1.7218/SCM430
-
Alloy Steel 8620/1.6523/20CrNiMoA/SNCM220
-
Alloy Steel 18CrNiMo7-6/17CrNiMo6/1.6587
-
Alloy Steel 18CrMo4/1.7243
-
Alloy Steel 30CrNiMo8/1.6580
-
Alloy Steel 36CrNiMo4/1.6511/SNCM439/EN24
-
Alloy Steel 34CrNiMo6/1.6582
Gears serve as critical components in a wide array of industrial applications, where they are subjected to substantial wear and tear during operation. To address this challenge, manufacturers often turn to 8620 steel due to its exceptional wear resistance, especially when subjected to appropriate heat treatment processes.
When heat-treated, 8620 steel undergoes transformations that significantly enhance its wear resistance. One key transformation is the formation of a durable surface layer with increased hardness. This surface layer, typically achieved through processes like carburizing or induction hardening, serves as a protective barrier against abrasive wear.
The hardened surface layer of 8620 steel effectively withstands the abrasive forces encountered during gear operation. Whether in heavy machinery, automotive transmissions, or power generation equipment, gears made from heat-treated 8620 steel exhibit prolonged service life and reduced susceptibility to wear-related failures.
By mitigating wear, 8620 steel contributes to prolonged gear operation and reduced maintenance costs. Gears equipped with 8620 steel components require less frequent replacements and maintenance interventions, leading to increased uptime and operational efficiency in industrial settings.
Cost-Effectiveness: Balancing Performance and Affordability
In the realm of high-performance alloys, 8620 steel stands out for offering a compelling balance between performance and affordability, making it a preferred choice for gear manufacturing across a spectrum of applications.
Despite the availability of specialized alloys with superior performance characteristics, the cost-effectiveness of 8620 steel is hard to overlook. Compared to these high-end alternatives, 8620 steel presents a significantly lower price point, making it an attractive option for manufacturers seeking to balance performance requirements with budgetary constraints.
What sets 8620 steel apart is its ability to deliver satisfactory performance levels without the premium price tag associated with specialized alloys. While it may not offer the absolute highest level of performance in terms of wear resistance or extreme temperature tolerance, 8620 steel provides a level of performance that meets the needs of many industrial applications.
Moreover, in scenarios where the highest level of performance is not a strict requirement, but durability and cost-effectiveness are paramount considerations, 8620 steel shines. Its reliable mechanical properties, coupled with its affordability, make it an ideal choice for applications where reliability and longevity are more critical than absolute performance benchmarks.
Applications of 8620 Steel Gears
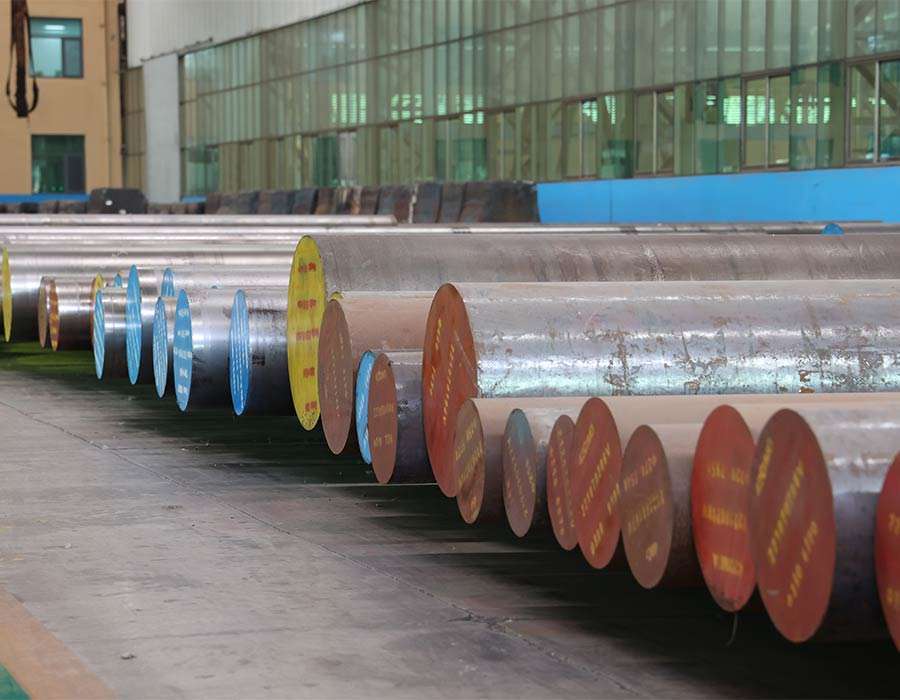
8620 steel gears find wide-ranging applications across industries such as automotive, aerospace, industrial machinery, and agriculture. From transmission gears in vehicles to gearboxes in heavy machinery, the versatility and reliability of 8620 steel make it a preferred material choice for demanding applications where precision and durability are paramount.
Conclusion
In conclusion, the properties of 8620 steel make it an ideal material for gear manufacturing. Its exceptional strength, toughness, wear resistance, and cost-effectiveness render it a top choice for gears operating in diverse industrial environments. By understanding the unique characteristics of 8620 steel, manufacturers can optimize gear performance, reliability, and longevity.
FAQs
Q: Can 8620 steel be welded?
A: Yes, 8620 steel can be welded using conventional welding techniques. However, it is essential to follow proper preheating and post-weld heat treatment procedures to minimize the risk of cracking and ensure adequate strength and toughness in the welded joints.
Q: What heat treatment processes are commonly used for 8620 steel gears?
A: Common heat treatment processes for 8620 steel gears include carburizing, quenching, and tempering. These processes are employed to achieve the desired combination of hardness, strength, and toughness required for specific gear applications.
Q: Are there any limitations to the use of 8620 steel in gear manufacturing?
A: While 8620 steel offers excellent mechanical properties for gear applications, it may not be suitable for extremely high-temperature environments where specialized heat-resistant alloys are required. Additionally, proper lubrication is essential to mitigate the risk of galling and wear in high-speed and high-load gear systems.
Q: What are the alternatives to 8620 steel for gear manufacturing?
A: Alternatives to 8620 steel include other low alloy steels such as 4140 and 4340, as well as specialized alloys like case-hardened steels, stainless steels, and various non-ferrous metals. The choice of material depends on specific application requirements, including operating conditions, load capacity, and cost considerations.