Introduction
Carbon tool steel refers to a variety of steel alloys that contain high amounts of carbon, typically around 0.5-1.5%. The carbon content provides these steels with excellent hardness and wear resistance, making them well-suited for tool and die applications. In this comprehensive guide, we will explore everything you need to know about carbon tool steels from their properties and processing to applications and comparisons with other tool steel varieties.
What Sets Carbon Tool Steels Apart?
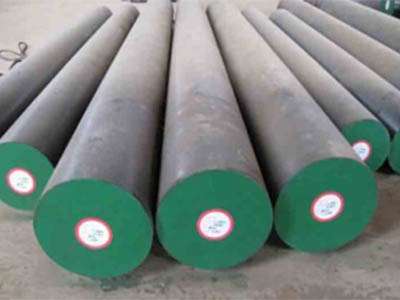
Carbon tool steels stand out from other types of tool steel thanks to their high carbon content. Here are some of the key properties provided by their carbon alloying:
- Excellent hardness (HRC 50-70) and wear resistance
- Good toughness and strength
- Resistant to deformation under load
- Ability to hold a sharp cutting edge
- Respond well to heat treatment
- Dimensional stability in heat treatment
In addition to carbon, carbon tool steels often contain other alloying elements like manganese, chromium, tungsten, and vanadium. This allows their properties to be tailored to specific applications.
Property | Advantage |
---|---|
Hardness | Resists wear and holds shape/edge |
Toughness | Resists chipping/cracking under force |
Strength | Handles cutting, pressing, stamping loads |
Thermal stability | Handles repeated heating/cooling cycles |
Compared to low carbon steels, carbon tool steels can better resist wear, hold shape at high temperatures, and remain hard through heat cycles like quenching and tempering. This makes them ideal where strength, hardness, and dimensional precision are critical.
Processing Carbon Tool Steels

There are a few primary methods used to process and shape carbon tool steels:
Casting – The steel is melted and poured into molds to produce ingots or near-net-shape castings. This allows complex tool geometries to be directly cast.
Forging – Cast ingots are heated and shaped under pressure by stamping or die pressing. Produces wrought shapes like bars, rods, and flats.
Machining – Forged tool steel stock is machined using processes like turning, drilling, and grinding to create shaped parts and finished tools.
Heat Treatment – Critical step where parts made of carbon tool steel are heated and cooled to develop desired metallurgical properties. Typically involves hardening followed by tempering.
Proper heat treatment is essential with carbon tool steels to reach optimal hardness, toughness, and dimensional stability. This usually consists of:
- Hardening – Heated then rapidly cooled to transform structure and increase hardness
- Tempering – Reheated to draw back some hardness for improved durability
The appropriate temperature and time parameters for hardening and tempering depend on the alloy composition and requirements of the particular steel grade.
Key Applications of Carbon Tool Steels
Thanks to their outstanding hardness, wear properties, and ability to hold shape and edges, carbon tool steels are used across countless demanding applications including:
Metal Forming – Forging dies, extrusion dies, mandrels
Cutting Tools – Turning tools, milling cutters, saw blades, drill bits
Stamping/Pressing – Blank, pierce, bend dies and tooling
Injection Molding – Cavity inserts, cores, compression screws
Woodworking – Cutters, knives, joining tools
Nearly any manufacturing processes that involve high pressures, temperatures, impacts, and complex shaping can benefit from carbon tool steel’s durability. They help tools stand up to punishing conditions and heavy mechanical loads over sustained production runs.
While specific grades excel in certain applications, widespread uses include:
- Punches and Die Components
- Forming and Pressing Tools
- Cutters and Knives
- Measuring Instruments
- Checking Fixtures
- Jigs and Fixtures
How Carbon Tool Steels Compare to Alternatives
Carbon tool steels have distinct advantages and disadvantages compared to other tool steel types:
Versus Alloy Steels – Carbon tool steels achieve higher hardness and wear resistance but lower toughness and shock resistance than chromium and tungsten alloy tool steels. They require more care during heat treatment and welding.
Versus High Speed Steels (HSS) – Carbon tool steels fall short of HSS in hardness, heat resistance, and cutting performance. But they are significantly less expensive to produce than these exotic powder metallurgy steels. Easier to machine as well.
Versus Die Steels – Cold and hot die steels offer the best combination of wear resistance, polishability, machinability, and thermal properties for die casting, forging, and extrusion applications. But carbon tool steels provide the highest sheer hardness and are cheaper.
So while they may lack specialty attributes of other tool steels, carbon tool steels deliver an unmatched balance of hardness, strength, toughness, and affordability.
An Overview of Common Grades
Many grades of carbon tool steel exist covering a spectrum of hardness, toughness, and applications. Several popular varieties include:
Grade | Description |
---|---|
A2 | General purpose cold work tool steel, combines hardness, toughness, and dimensional stability, popular for stamps and dies |
A6 | Oil hardening tool steel, offers maximum shock resistance with high hardness and strength for high-impact cold forming |
A8 | Less alloyed cold work steel, cheaper alternative to A2 but with shorter tool life, used for shear blades and presses |
A9 | Special purpose oil hardening steel, enhanced polishability and machinability good for intricate dies and tools |
D2 | Very high carbon/chromium tool steel, used for cold work punches, forming rolls, and drawing dies requiring extreme hardness |
S7 | Shock resisting tool steel, highest impact toughness combined with good wear resistance for hammers, presses, drive shafts |
These represent just a sampling as many additional grades like H13 exist, each optimized with slight alloy adjustments for attributes like hardenability, polishability, toughness, machinability etc.
Conclusion & Summary
With exceptionally high hardness ratings along with good toughness and thermo-mechanical stability, carbon tool steels have become indispensable across metal manufacturing. Their high carbon alloys provide the wear resistance necessary for punishing cold work applications involving shaping, pressing, extruding, and cutting. They respond very well to heat treatment which allows their properties to be dialed in precisely for the intended service conditions and loads.
While costing more than lower carbon steels, carbon tool steels provide outstanding value relative to other specialty tool steel options. Their balance of hardness, strength, and affordability makes carbon tool steel suitable for the majority of tooling needs. Continual development of newer alloys along with advances in steel melting, casting, powder metallurgy, and heat treatment will ensure carbon tool steels remain a staple material across production environments for generations to come.
FAQ
What heat treatment processes are used on carbon tool steels?
Carbon tool steels are typically put through a sequence of hardening followed by tempering. Hardening involves heating to a high austenizing temperature then rapidly cooling or quenching to transform the microstructure. Tempering reheats the steel to a lower temperature to draw back some hardness in exchange for improved toughness and reduced brittleness.
Are carbon tool steels weldable?
Most carbon tool steels can be welded but it requires special preheating and post-heating procedures to avoid cracking. Their high carbon content also means they must be welded with low hydrogen processes. Stress relieving and re-hardening heat treatments are also usually needed post-weld to retain proper metallurgical properties.
What affects the properties and performance of carbon tool steels?
A few key factors influence carbon tool steel properties including alloy composition, heat treatment parameters, machining and grinding quality, and surface treatments/coatings. Precise control over chemistry, microstructure, heat processing, machining, and secondary treatments all cumulatively determine the final tool steel performance in service. Very small deviations can significantly impact tool life.
How should carbon tool steels be machined and ground prior to heat treatment?
The hardest machining and grinding should be performed prior to heat treatment when the steel is in a softer annealed state requiring less powerful equipment. Rough machining, drilling, tapping, and aggressive surface grinding can all be efficiently accomplished before hardening and tempering makes the steel extremely difficult to cut and machine conventionally requiring diamond tooling.