Introduction
Tool steels refer to a variety of ultra-hard steels optimized for making cutting, pressing, and forming tools. They retain hardness and shape at high temperatures, resist wear, and withstand impact stresses encountered during manufacturing processes. Hundreds of unique tool steel types exist – each fine-tuned through careful alloying to excel in specific applications.
This guide serves as a broadly inclusive tool steel overview. We’ll survey critical properties then contrast major categories and review examples from widely used grades. A fuller appreciation of the capabilities of the various tool steel types supports matching the optimal grade to your tooling challenge.
The Essential Qualities of Tool Steels
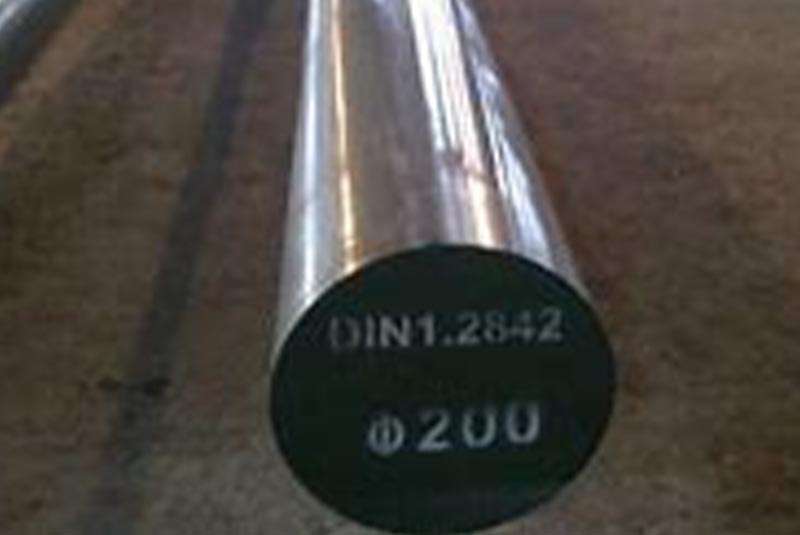
All tool steels leverage combinations of the following characteristics:
- Extreme hardness to resist deformation
- Strength to withstand service loads
- Toughness to resist chipping and fracture
- Wear resistance to combat abrasion and adhesion
- Dimensional stability across temperature fluctuations
- Hardenability for heat treating large cross sections
Tuning relative levels of these attributes allows toolmakers to tailor steel grades capable of overcoming specific wear mechanisms and challenging environmental conditions encountered in manufacturing and metalworking.
Property | Unit of Measurement | Test Methods |
---|---|---|
Hardness | HRC (Rockwell C) | Scales, Indenters |
Strength | MPa, psi (Yield, UTS) | Tension,Compression |
Toughness | ft-lbs, J (Impact energy) | Izod, Charpy |
Wear Resistance | Hardness, HRC | Abrasion Tests |
Dimensional Stability | 10^-6 in/in/°F | Dilametry |
Hardenability | Jominy End-Quench | CCT Diagrams |
The premium performance comes from carefully balancing primary elements like tungsten, molybdenum, vanadium, and cobalt with carbon and iron – but no two formulas are alike.
Contrasting Major Tool Steel Categories
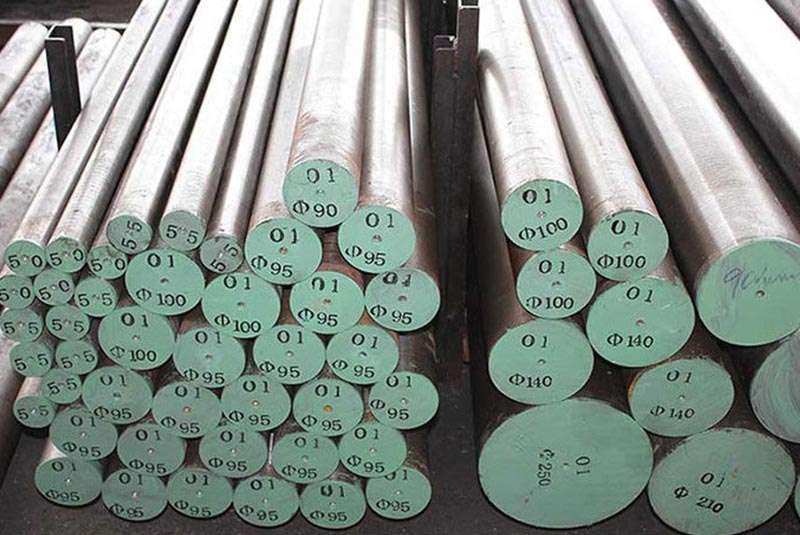
Tool steels group into several major categories:
Water Hardening – An early variety relying primarily on high carbon content to facilitate through hardening. Limited use today.
Shock Resisting – Made exceptionally tough by increasing manganese and silicon levels. Used for high impact cold work tools like chisels and punches.
Cold Work – Very versatile general-purpose tool steel able to combine wear resistance with durability thanks to intermediate alloy content. Common in blanking/forming dies.
Hot Work – More heavily alloyed for elevated temperature strength and thermal stability. Extensively used for hot extrusion dies and forging tooling.
High Speed Steel – Alloyed with large amounts of tungsten, molybdenum, and vanadium enabling exceptional hardness and cuttability up to red heat. Dominates cutting tools.
Special Purpose – Encompasses proprietary vendor grades formulated for niche applications like superior polishability or machinability. Newer powder metallurgy tool steels also belong here.
Summarizing key high-level differences aids in narrowing suitable candidates but granular analysis of alloy composition and treatment specifics ultimately guides proper tool steel section.
Review of Widely Used Tool Steel Grades
Literally thousands of tool steel subvarieties exist but several popular examples in each category include:
Shock Steels
- S7 – exceptional impact strength and wear resistance for cold header tooling
- S5 – high toughness and hardness balance for punch/die sets
Cold Work Steels
- A2 – versatile general-purpose cold work steel combining wear resistance and durability
- D2 – high carbon and chromium for severe stamping and blanking applications
- O1 – an oil hardening grade valued for uniform hardness and machinability
Hot Work Steels
- H13 – industry mainstay hot work steel with best all-around properties
- H11 – similar alloy to H13 but with better machinability and polishability
High Speed Steels
- M2 – widely regarded as the benchmark high speed steel grade
- M35 – cobalt bearing high speed steel for high heat applications
- M42 – powder metallurgy high speed steel granting fine grain size control
This sampling provides a set of incumbent workhorse tool steel varieties along with more recent powder metallurgical and exotic grades. New candidates continually emerge claiming further incremental performance gains as tool steel technology continues advancing.
Key Tool Steel Applications
Tool steels facilitate practically all subtractive, additive, and formative manufacturing processes. Some prominent examples include:
- Cutting – drills, taps, reamers, milling cutters, saw blades
- Metal Removal – blanking, piercing, trimming, and slitting dies; nibbling cutters
- Forming & Shaping – benders, punch/press tooling, headers, stamps, draw dies
- Casting & Molding – injection molds, extrusion dies, blow molding tooling
Different tool steel types shine across specific processes based on stresses and temperatures experienced. So comprehensively reviewing tool operating conditions provides key inputs when selecting ideal grades.
Picking the Right Tool Steel Type
Choosing the optimal tool steel variety seems a daunting task but simply involves:
- Documenting design parameters:
- Operating temperatures
- Production run length
- Tolerances
- Target hardness
- Identifying failure modes to avoid:
- Wear, abrasion
- Fatigue and cracking
- Plastic deformation
- Corrosion pitting
- Referencing alloy comparisons across tool steel types to pinpoint 2-3 best suited candidates
- Performing final grade validation with heat treatment trials
While ultra-high performance grades tempt specification, balance performance with cost by leveraging existing proven alloys whenever feasible. Partnership with an experienced tool steel provider simplifies navigation of this decision process.
The Future of Tool Steel Development
Ongoing innovation promises exciting tool steel improvements on the horizon:
- Novel compositions for extreme environments like high speed machining
- Powder steels using nanoparticle blends to push limits of properties
- Sophisticated modeling to predict in-service performance
- Hybrid additive/conventional fabrication approaches
- Automating optimization of heat treatment
Through persistent tool steel research and progress, expect machiningproductivity, part quality, and tool longevity to continue advancing across manufacturing.
Conclusion & Summary
From ubiquitous cold work varieties to highly specialized powder metal grades, tool steel selection spans a complex landscape filled with attractive options. Simplifying analysis requirements into quantifiable performance criteria and known failure modes makes navigating choices more manageable. Partnering with trusted tool steel suppliers also lends expertise. Regardless of methods, appropriate steel grade specification remains absolutely essential for tooling and die components tasked with shaping each next generation of advancing materials – tool steels included.
FAQ
What is the main advantage of using tool steels over alloy and structural steels?
Tool steels differentiate themselves from more common alloy/structural grades by offering superior hardness, wear properties and high temperature strength specifically targeted to withstand the extreme pressures, temperatures, and abuse encountered across metal manufacturing processes.
Do tool steels feature increased toughness versus stainless steels?
No. Stainless steels generally demonstrate higher base toughness values compared to tool steel varieties – especially the shock and high speed steel families. However, certain cold work and hot work tool steel alloys close this gap substantially while still providing the requisite hardness necessary.
Why are there so many specialized tool steel grades instead of just a few high performing types?
The wide range exists because no single tool steel type offers optimal performance across all fabrication processes. Unique compositions evolve targeting the differing temperatures, stresses, and wear patterns distinctive to categories of manufacturing – hot versus cold forming processes being a notable example. Developing improved alloys persists as new materials and methods emerge.