Introducción
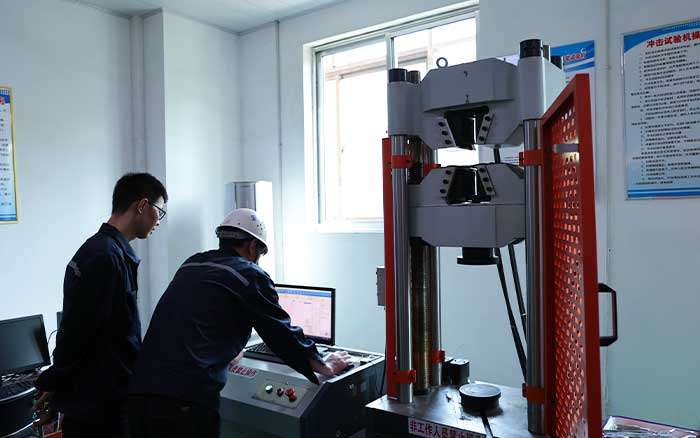
In the world of metallurgy, D2 acero stands out for its exceptional hardness and durability. In this comprehensive guide, we delve deep into the intricacies of D2 steel hardness levels, exploring its properties, applications, and significance in various industries.
Understanding D2 Steel: An Overview
In this section, we embark on an insightful journey into the realm of D2 steel, a high-carbon, high-chromium tool steel renowned for its exceptional hardness and wear resistance. We begin by unraveling the intricate composition of D2 steel, which typically consists of approximately 1.5% carbon, 12% chromium, 1% molybdenum, and other alloying elements such as vanadium and manganese. This carefully crafted alloy composition imparts unique properties to D2 steel, making it a preferred choice for a wide range of industrial applications.
Furthermore, we shed light on the meticulous manufacturing process that transforms raw materials into D2 steel of unparalleled quality. From the initial melting and refining stages to the precise heat treatment procedures, every step plays a crucial role in shaping the final properties of D2 steel. Through controlled cooling and quenching, the steel attains its distinctive hardness and microstructure, setting it apart as a formidable material in the realm of engineering and manufacturing.
Delving deeper, we explore the notable characteristics that distinguish D2 steel from other alloys. Beyond its impressive hardness, D2 steel exhibits exceptional wear resistance, edge retention, and dimensional stability, making it highly coveted in applications where durability and precision are paramount. Moreover, its resistance to deformation and corrosion further elevate its suitability for demanding environments, ensuring longevity and reliability in various industrial settings.
Exploring D2 Steel Hardness Levels
In this section, we embark on a detailed exploration of the hardness spectrum within D2 steel, a crucial aspect that defines its suitability for various applications. Our journey begins with an examination of the Rockwell hardness scale, a widely utilized method for quantifying the hardness of metallic materials. By understanding the intricacies of this scale, including its testing procedures and numerical representations, we lay the groundwork for comprehending the hardness levels exhibited by D2 steel.
Furthermore, we delve into the significance of the Rockwell hardness scale in the context of D2 steel, elucidating how it serves as a reliable indicator of the alloy’s mechanical properties. Through precise indentation testing and subsequent measurement, engineers and metallurgists can accurately assess the hardness of D2 steel, facilitating informed decision-making in material selection and process optimization.
As we delve deeper into the realm of D2 steel hardness, we uncover a diverse spectrum of hardness levels that characterize this alloy. From relatively moderate hardness values to exceptionally high levels, D2 steel exhibits a versatility that caters to a wide range of industrial requirements. Through empirical data and case studies, we showcase the variability of D2 steel hardness across different heat treatment conditions, grain structures, and alloy compositions, offering valuable insights into its performance characteristics under various operating conditions.
Factors Influencing D2 Steel Hardness
In this section, we embark on a comprehensive exploration of the multifaceted factors that intricately shape the hardness of D2 steel, a critical aspect that profoundly influences its performance and applicability across diverse industries. Our journey delves into the intricate interplay of various variables, ranging from the intricacies of heat treatment methods to the subtle nuances of alloying elements, all of which exert a profound impact on the final hardness properties exhibited by D2 steel products.
Firstly, we unravel the pivotal role of heat treatment methods in the determination of D2 steel hardness. From annealing to quenching and tempering, each stage of the heat treatment process imparts distinct microstructural changes that directly influence the hardness profile of D2 steel. By meticulously controlling parameters such as temperature, time, and cooling rates, metallurgists can tailor the hardness characteristics of D2 steel to meet specific performance requirements, striking an optimal balance between hardness, toughness, and machinability.
Furthermore, we delve into the intricate chemistry of alloying elements present in D2 steel, each contributing its unique imprint on the final hardness properties of the alloy. Chromium, molybdenum, vanadium, and carbon are among the key alloying elements that play a pivotal role in enhancing the hardness, wear resistance, and corrosion resistance of D2 steel. Through a nuanced understanding of their interactions and synergies, metallurgists can fine-tune the composition of D2 steel to achieve desired hardness levels while ensuring optimal mechanical properties and performance characteristics.
Applications of D2 Steel Hardness
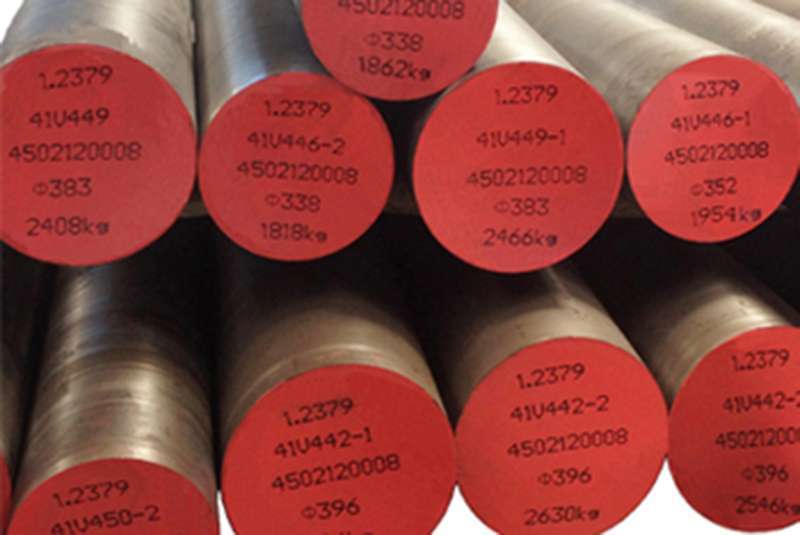
In this section, we embark on a captivating journey through the myriad of industries where the exceptional hardness of D2 steel finds invaluable applications, showcasing its versatility and indispensability in a wide array of fields. From the precision-driven realm of tool and die making to the intricate craft of knife manufacturing, D2 steel hardness stands as a hallmark of excellence, elevating performance and durability to unparalleled heights.
Starting with the realm of tool and die making, D2 steel emerges as a cornerstone material renowned for its ability to withstand the rigors of high-stress environments with unwavering resilience. Whether in the fabrication of stamping dies, extrusion tools, or forming punches, the exceptional hardness of D2 steel imparts superior wear resistance, edge retention, and dimensional stability, ensuring prolonged service life and unmatched precision in critical manufacturing processes.
Venturing into the realm of knife manufacturing, D2 steel hardness reigns supreme as a preferred choice among discerning craftsmen and enthusiasts seeking uncompromising quality and performance. Renowned for its razor-sharp edge retention, exceptional toughness, and corrosion resistance, D2 steel transforms ordinary knives into formidable tools capable of withstanding the most demanding cutting tasks with effortless precision and reliability.
Comparison with Other Steel Alloys
In this section, we compare the hardness levels of D2 steel with other popular steel alloys. Through comparative analysis and data-driven insights, we provide readers with a comprehensive understanding of how D2 steel stacks up against its counterparts.
Steel Alloy | Hardness Range (Rockwell C) | Notable Characteristics |
---|---|---|
Acero D2 | 58-62 HRC | Exceptional hardness, wear resistance, and toughness |
D3 Steel | 60-64 HRC | High hardness, good edge retention, and toughness |
T10 Tool Steel | 59-61 HRC | Excellent toughness, wear resistance, and machinability |
T8 Tool Steel | 63-65 HRC | Superior hardness, edge retention, and wear resistance |
Conclusión
In conclusion, we summarize the key takeaways from our exploration of D2 steel hardness levels. We emphasize the importance of understanding hardness in steel and how it influences the performance and applications of D2 steel in real-world scenarios.
PREGUNTAS FRECUENTES
What is the typical hardness range for D2 steel?
We discuss the typical hardness range for D2 steel and factors that may influence variations in hardness levels.
How does heat treatment affect the hardness of D2 steel?
We explore the impact of heat treatment on D2 steel hardness and the importance of proper heat treatment processes.
Can D2 steel be hardened to different hardness levels?
We address whether D2 steel can be customized to achieve specific hardness levels based on application requirements.