Introducción
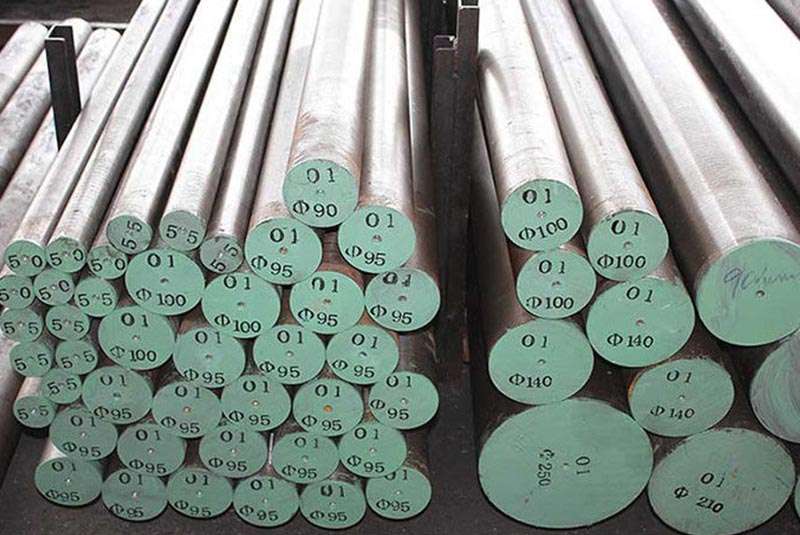
The composition of the tool steel is very important in use,when engineers seek specialized steel grades balancing extremely high hardness for wear resistance while retaining adequate toughness across applications ranging from cutting blades to plastic mold tooling, tool steel alloys become the top material choice. Unlike structural steels prioritizing flexibility and weldability, tool steels uniquely derive their characteristic combination of exceptional strength and durability from selectively blended compositions of carbon and specific alloying elements formulated to bestow tailored physical and microstructure properties. This article illuminates the function key constituents like tungsten, chromium and vanadium serve within tool steel chemistry alongside processing techniques for unlocking customized properties.
The Vital Role of Carbon
The foundation of all tool steel grades begins with optimizing percentages of carbon, the primary hardening element:
● Interstitially occupies spaces within iron lattice structure:Interstitially occupying spaces within the iron lattice structure refers to the insertion of atoms or molecules into the gaps or interstices between the iron atoms in the lattice. This process involves the incorporation of foreign atoms, such as carbon or nitrogen, into the lattice structure of iron, where they reside in the spaces between the iron atoms. By occupying these interstitial sites, the foreign atoms can influence the mechanical and chemical properties of the iron, altering its hardness, strength, and other characteristics. This phenomenon is particularly significant in the context of alloying iron to create steel, where the interstitial atoms play a crucial role in defining the properties of the resulting material.
● Restricts dislocation movements thereby drastically escalating strength:By impeding the movement of dislocations, the material significantly enhances its strength. Dislocations are defects or irregularities in the crystal lattice of a material that can move and propagate under stress, leading to plastic deformation. When the movement of dislocations is restricted, either by the presence of alloying elements or by other mechanisms, the material’s resistance to deformation and fracture increases substantially. This restriction of dislocation movement effectively reinforces the material’s structure, preventing the formation of plastic flow and promoting higher levels of strength. As a result, the material becomes more capable of withstanding external forces and maintaining its structural integrity, making it suitable for applications where strength and durability are paramount.
● Improves hardness capacity from just 200HV to over 800HV (Vickers Scale):Enhancing the hardness capacity from a mere 200HV to over 800HV (Vickers Scale) represents a significant improvement in the material’s resistance to indentation and wear. This substantial increase in hardness is achieved through various methods, such as alloying, heat treatment, and surface treatments. By introducing alloying elements or altering the microstructure of the material, it becomes possible to strengthen the material’s lattice structure, thereby increasing its resistance to plastic deformation and improving its ability to withstand abrasive forces. This enhanced hardness not only prolongs the lifespan of the material but also expands its range of applications, allowing it to excel in environments where wear and abrasion are prevalent. Overall, the improvement in hardness capacity signifies a substantial advancement in material science and engineering, opening doors to new possibilities in various industries.
● Simultaneously reduces innate ductility and weldability in higher proportions:Simultaneously reducing the intrinsic ductility and weldability, particularly in higher proportions, signifies a trade-off in material properties. While enhancing certain aspects like hardness and strength, this reduction in ductility and weldability can result from changes in the material’s microstructure, alloying elements, or processing techniques. Decreased ductility means the material is less able to deform plastically before fracturing, which may affect its formability and toughness. Similarly, diminished weldability implies challenges in achieving strong and reliable weld joints, potentially limiting fabrication options. Therefore, it’s crucial to carefully consider the balance between desired mechanical properties and potential drawbacks when optimizing material composition and processing for specific applications.
This interplay allows tuning percentages between 0.70-1.50% balancing tremendous hardness and sufficient impact toughness as per individual tool functionalities.
Alloying Elements’ Contribution
To further amplify properties, measured additions of alloying elements then selectively create tool steel families with amplified capabilities:
Elemento de aleación | Key Attribute Improved | Tool Steel Family |
---|---|---|
Tungsten | Heat and wear resistance | High speed steel |
Molibdeno | High temperature strength | Hot working steel |
Vanadium | Fine grain structure | Cold working steel |
Cobalt | Hot hardness retention | Milling tool steel |
The intensely concentrated carbide compounds formed by these elements enhance specific traits like heat treatability, temper resistance etc dramatically.
Compositions Matched to Tool Requirements
By manipulating the assorted special purpose alloying elements, tool steel metallurgists tailor compositions delivering macrostructures and associated properties aligned to individual tool applications through:
Tool Type | Desired Properties | Composition Example |
---|---|---|
Cutters | Exceptional hardness | 1.4% C, 18% W, 6% Cr |
Troqueles | High strength; Toughness | 0.35% C, 0.8% Mo, 3%Ni |
Gauges | Consistent machinability | 0.6% C, 0.5% Mn, 0.25%S |
Heat Treatment Activation
While chemistry provides latent capability, only heat application awakens tool steel potential through:
● Hardening – Rapid heating then quenching sets up desired phases
● Tempering – Controlled low temperature heating restores limited ductility
When combined with mechanical deformation techniques like cold working, manufacturers extract optimized physical properties from the enriched chemical compositions.
Economic Implications of Compositions
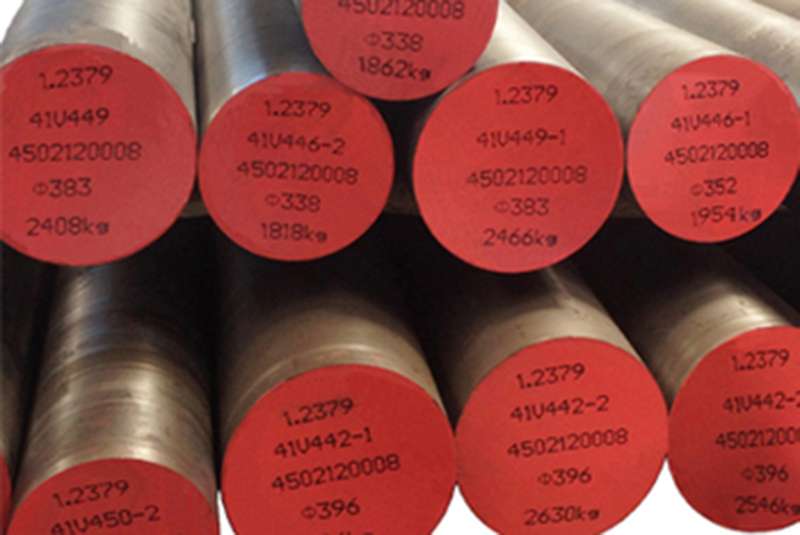
Pursuing enhanced tool steel compositions does impact procurement costs through:
● Alloying – Specialty tungsten grades and processing add cost.
● Energy intensity – Complex controlled atmosphere heat treatment.
● Machinability – Uniform fine grain structure needs pre-machining.
However, the huge asset durability and productivity payoff outweigh initial investments for most tool operations.
Conclusion:Tool Steel Composition
● Optimized carbon establishes the backbone of tool steel property capabilities:The optimized carbon content serves as the foundational element that underpins the diverse capabilities and properties of tool steel. By fine-tuning the carbon composition, tool steel achieves enhanced strength, durability, and versatility, ensuring it meets the rigorous demands of various industrial applications.
● Alloying ingredients like tungsten and chromium boost particular attributes:Incorporating alloying elements such as tungsten and chromium elevates specific characteristics within the tool steel. Tungsten enhances hardness and wear resistance, ideal for applications requiring durability and cutting performance. Chromium contributes to improved corrosion resistance and oxidation resistance, particularly beneficial in harsh operating environments. Together, these alloying ingredients augment the overall properties of the tool steel, ensuring it meets the diverse requirements of different industries and applications.
● Harnessing metallurgical mechanisms creates custom property profiles:Utilizing metallurgical mechanisms enables the creation of tailored property profiles in tool steel. By harnessing techniques such as alloying, heat treatment, and microstructure control, manufacturers can engineer specific combinations of strength, toughness, hardness, and other properties to meet the unique requirements of diverse applications. This customization empowers industries to optimize tool steel performance for their specific operational needs, ensuring enhanced efficiency, reliability, and longevity in various manufacturing processes and applications.
● Attaining the best lifecycle value requires balancing alloying expenses against reliability services rendered:Achieving optimal lifecycle value entails striking a balance between investment in alloying elements and the reliability of services provided by tool steel. While alloying expenses contribute to enhancing the material’s performance and longevity, it’s crucial to weigh these costs against the benefits derived from the steel’s reliability in real-world applications. By carefully managing alloying expenses and leveraging the durability and efficiency of tool steel, industries can maximize their return on investment over the entire lifecycle of their equipment and components. This strategic approach ensures cost-effectiveness and sustainability while maintaining high standards of performance and reliability.
Equipped with this comprehensive perspective encompassing interacting chemical, physical and economic dynamics within tool steel compositions, engineers can confidently specify the optimal make-up foundation delivering exceptional combined strength and resilient properties that stand up to the intense demands of shaping operations over prolonged use cycles.
Preguntas frecuentes
Q:How do cobalt particles enable hot hardness retention?
At elevated temperatures, tool steel restrains movement by forming intricate carbides within its evolving crystal structure. This phenomenon effectively prevents softening, ensuring that the material retains its strength and integrity even under challenging thermal conditions. The formation of complex carbides acts as a barrier against deformation, maintaining the tool steel’s mechanical properties and allowing it to withstand high temperatures without compromising performance. This mechanism is crucial in applications where stability and durability are paramount, enabling tool steel to excel in demanding environments such as high-temperature machining and forging operations.
Q:What determines the limits for maximizing alloying elements like tungsten?
The metallurgical composition imposes solubility limitations, particularly regarding tungsten content. Exceeding approximately 18% tungsten can lead to the formation of undesirable brittle phases within the material. These brittle phases compromise the integrity and mechanical properties of the tool steel, rendering it susceptible to cracking and failure under stress. Therefore, maintaining tungsten content below the critical threshold is essential to prevent the formation of these detrimental phases and ensure the desired balance of strength, toughness, and ductility in the tool steel. This careful management of alloy composition is crucial for optimizing the performance and reliability of tool steel in various industrial applications.
Q:What property change drove the evolution from conventional tool steels to powder metallurgical grades?
The pursuit of higher hardness levels while maintaining fracture resistance has driven the adoption of blended fine grain powder processing techniques. This innovative approach involves combining fine-grained powders of different compositions to achieve a precise balance of hardness and toughness in the final tool steel product. By blending powders with varying properties, manufacturers can tailor the microstructure of the material to enhance both its hardness and fracture resistance simultaneously. This allows for the production of tool steel with exceptional performance characteristics, capable of withstanding high levels of wear and impact without succumbing to brittle fracture. Blended fine grain powder processing represents a significant advancement in metallurgical technology, enabling the development of tool steel with unparalleled strength and durability for demanding applications in various industries.